How to get the ultra-effective microspeaker?
- REINCHEM
- 2022-01-10
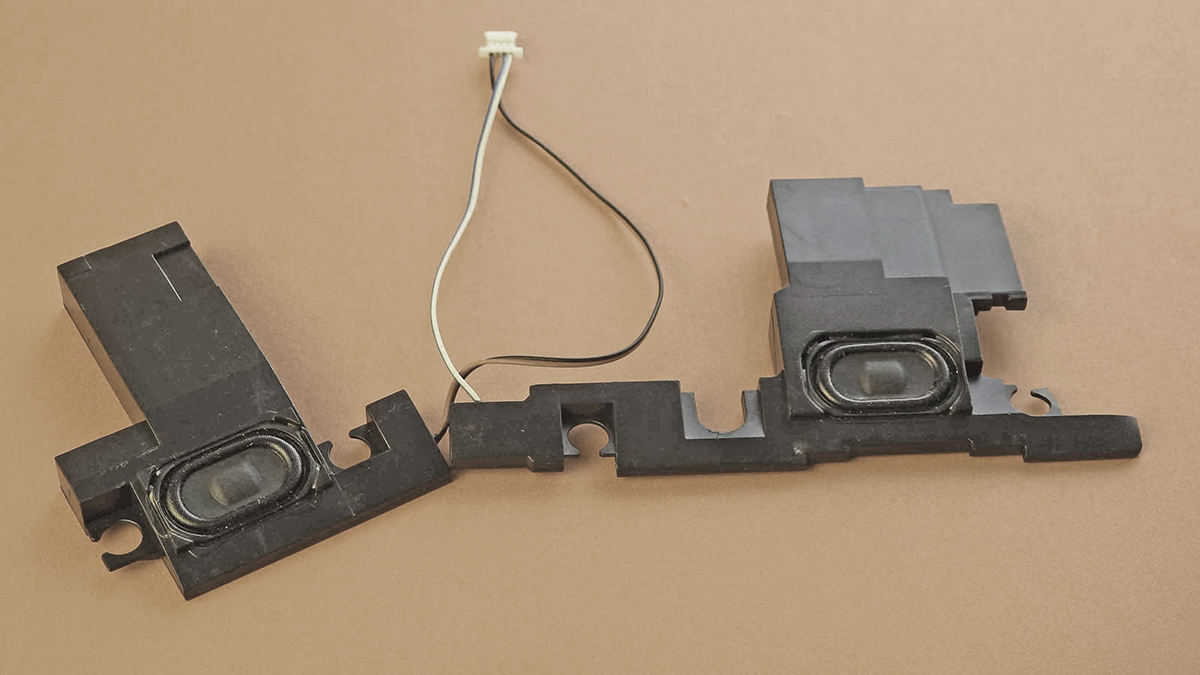
Specifically:
1. Cost based on the huge amount.
2. Sound volume behind the speaker
3. Good speaker sensitivity, low battery consumption
4. "Line of sight" between the front of the speaker and the listener
5. Sufficient amplifier power, low power consumption and low heat
Efforts to reduce footprint and depth continue, but the depth of the miniature speaker (Z axis) has dropped from 3millimeters in smartphones to 2.5millimeters due to the removal of the 3.5-millimeter headphone jack, which has been the bottleneck. The same product development teams that demanded increased efficiency, power handling, clearer sound, and extended bass and high-end response also demanded the lowest possible price.
In the composition of the micro speaker unit, the diaphragm is one of the most important components affecting the sound quality. The factors of the diaphragm on the influence of sound quality can be roughly divided into 2 major categories: one is the shape factor, which includes the caliber, the depth of the diaphragm, reinforcement, bus shape, material thickness, etc.; the second is the material factor, which includes the characteristics of the material, processing technology, manufacturing methods, and others. The above 2 categories of factors affect the resonant frequency of the speaker, power range, frequency response curve trend and smoothness.
The current structural form of cell phones and other microspeakers is the diaphragm with the top dome structure design, the dome needs to have a good specific stiffness and damping characteristics. The most optimized structure and material system of dome is the ultra-thin composite sandwich structure of metal surface layer combined with PMI foam core.
![]() |
![]() |
Composites are materials with a structure of two or more phases, where each phase maintains essentially the same physical and chemical properties.
The sandwich structure is generally composed of upper panel, bonded layer of upper panel and core, core, bonded layer of lower panel and core, and lower panel, and these five elements form a whole sandwich structure. The way of load transfer of the sandwich structure is similar to that of an I-beam, where the upper and lower panels (wings) are mainly subjected to in-plane tensile and in-plane shear stresses caused by bending moments, while the core material (web) is mainly subjected to shear stresses generated by transverse forces.
In order for the elements of the sandwich structure to carry the load synergistically, the bonding layer between the panel and the core must be able to transfer the load so that it should have at least the same strength as the core. Choosing the right adhesive also has a very important significance to the strength of the sandwich structure. Usually, when choosing an adhesive, in addition to the strength, it is necessary to consider the use of temperature, smoke conditions and its compatibility with the panel material of the core. If you choose to co-cure with the panel material, the curing conditions of the adhesive or adhesive film need to be consistent with the co-curing conditions of the panel.
PMI is the strongest and stiffest foam for the same density. Its creep resistance at high temperatures makes it suitable for high temperature curing resins and prepregs. PMI foam is made by solid foam process, which is a rigid foam with basically uniform pores and more than 99% of uniform closed cell rate. Currently, ARCHCELL® of Shanghai Lanin is available in the market with perfect specifications.
ARCHCELL® is the trademark of Shanghai ReinChem's PMI foam.
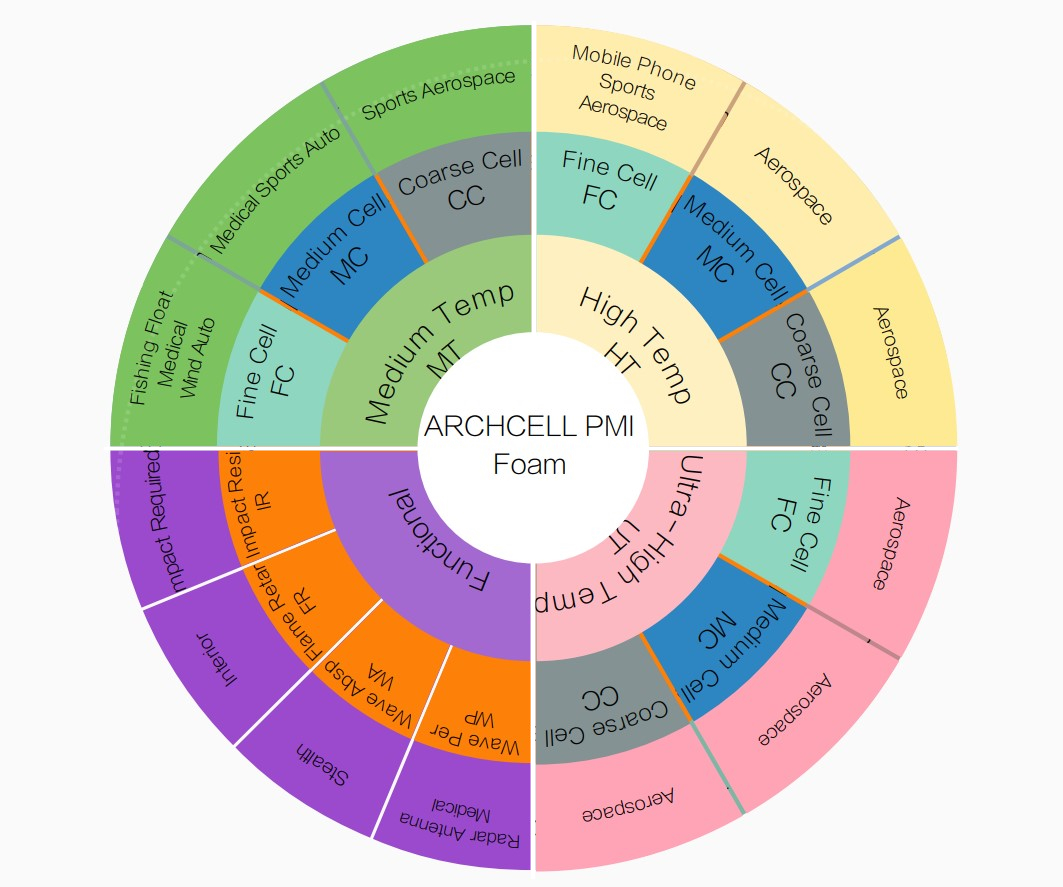
ARCHCELL® is mainly divided into two categories, one is structural foam, which is distinguished according to heat deflection temperature; and the other is functional foam, which currently has four main types: wave-transparent, wave-absorbing, flame retardant and impact resistant.
The PMI foams currently available for dome materials for micro speakers are, HT fine hole, UT fine hole, IR type and WP type, with different temperature resistance, different fracture elongation and void size respectively, suitable for various processing processes and glue systems.
With its own ultra-thin carbon fiber prepreg and innovative process, it has developed the next generation of ultra-thin carbon fiber PMI foam sandwich structure 3D shaped dome.
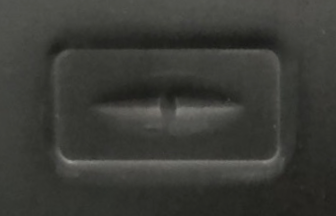